In today’s competitive business environment, companies need to constantly evaluate and improve their operations to stay ahead of the competition. Two essential frameworks for achieving this are the value chain and supply chain. While both supply and value chain is critical to a company’s success, they serve different purposes and involve different activities.
In this blog post, we will discuss both the value chain and supply chain, provide examples of how companies can create value and optimize their operations, and highlight the differences between the two frameworks. Additionally, we will explore how companies can integrate the value chain and supply chain to achieve better performance and sustain a competitive edge in the market.
Value Chain
Definition of Value Chain
A value chain is a framework used to analyze a company’s activities and processes involved in transforming inputs into an end product or service. Value chains were introduced by Michael Porter, a renowned business strategist, in his book “Competitive Advantage.” According to Porter, a value chain consists of a set of activities that add value to the product or service and enable a company to achieve a competitive advantage.
Explanation of the Components of the Value Chain
The value chain activities consist of five primary activities and four support activities. The primary activities are logistics, operations, marketing, sales, and service. The support activities of a value chain are technology development, human resources management, procurement, and firm infrastructure.
1. Inbound Logistics
Inbound logistics involves the activities required to receive, store, and distribute raw materials or other inputs needed to produce an end product or service. This includes activities such as transportation, warehousing, and inventory. By effectively managing these logistics, companies can lower costs and ensure a reliable supply of high-quality raw materials.
2. Operations
Operations refer to the activities in transforming inputs into an end product or service. This includes manufacturing, assembling, and testing of products, as well as the provision of services. Operational management involves optimizing processes and workflows to increase efficiency, reduce waste, and improve the quality control of the end product or service.
3. Outbound Logistics
Outbound logistics involves the activities required to store, distribute, and deliver the end product or service as per the customer’s request. This includes transportation, warehousing, and order processing. By optimizing outbound logistics, companies can ensure timely delivery, lower costs, and improve the entire supply chain.
4. Marketing and Sales
Marketing and sales refer to the activities in promoting and selling the end product or service to customers. This includes market research, advertising, sales, and customer support. By effectively managing marketing and sales activities, companies can create demand for their products or services, increase revenue, and improve a company’s supply chain.
5. Service
Service refers to the activities performed in providing after-sales services to customers, such as repairs, maintenance, and customer support. Effective service management can help companies build strong customer relationships, increase customer loyalty, and generate repeat business.
Examples of How Companies Can Create Value in Each Component of the Value Chain
Companies can create value in each component of the value chain by conducting a value chain analysis and implementing strategies that improve efficiency, lower costs, and enhance customer value. For example, a company could implement lean manufacturing practices to optimize its operations, reduce waste, and improve the quality control of its products. Additionally, by implementing effective value chain management with inbound value chain strategies, such as just-in-time inventory, a company can minimize the amount of inventory it holds, lower costs, and ensure a reliable supply of high-quality raw materials.
Importance of Understanding and Managing the Value Chain
Understanding and managing value chain is critical for user satisfaction and gaining a competitive advantage. By optimizing each component of the value chain concept, companies can be focused on overall business management and on minimizing costs, improving quality of every product request, and ensure customer satisfaction with a well-made finished product. By effectively managing the value chain, companies can achieve operational excellence, meet consumer demand, and deliver high-quality products and services from an operational management perspective.
Supply Chain
Definition of Supply Chain
The term supply chain refers to the network of organizations, activities, resources, and technologies involved in the creation and delivery of a product or service to the user. The supply chain begins with the acquisition of raw materials and ends with the delivery of the end product or service to the user.
Explanation of the Components of the Supply Chain
The supply chain facilitates sustaining superior performance of five key components, which are planning, sourcing, making, delivering, and returning.
1. Planning
Supply chain starts with planning, which involves forecasting demand, determining the required inventory levels, and creating a production schedule to ensure that the right products are available at the right time. Effective planning can help companies improve customer experience, minimize costs, and reduce waste.
2. Sourcing
Sourcing refers to the process of identifying and selecting suppliers who can provide the required raw materials, components, or services needed to create the end product. By selecting the right suppliers, companies can ensure the quality of the raw materials or components, lower costs, and ensure timely delivery.
3. Making
Making involves the transformation of raw materials or components into a finished product or service. This includes manufacturing, assembling, and testing of products, as well as the provision of services. Effective production management can help companies optimize processes, reduce waste, and improve the quality of the end product or service.
4. Delivering
Delivering involves the transportation and distribution of the final product or service to the end-user. This includes activities such as transportation, warehousing, and order processing. By optimizing the delivery process, companies can ensure timely delivery, lower costs, and improve customer satisfaction.
5. Returning
Returning involves managing the reverse flow of products or services from the end-user back to the company. This includes activities such as product recalls, repairs, and returns. Effective management of the return process can help companies lower costs, improve customer satisfaction, and maintain their reputation.
Examples of How Companies Can Optimize Their Supply Chain
Companies can optimize their supply chain activities by implementing strategies that improve efficiency, reduce costs, and enhance customer value. For example, by implementing effective demand forecasting techniques, companies can ensure that they have the right amount of inventory at the right time, minimizing inventory costs while meeting customer demand. Additionally, by optimizing the delivery process, companies can reduce transportation costs and improve delivery times, enhancing customer satisfaction.
Importance of Understanding and Managing the Supply Chain
Understanding and managing the supply chain includes companies seeking to sustain impressive performance and gain a competitive advantage. By optimizing each component of the supply chains, companies can reduce costs, improve quality, and enhance customer value. Effective supply chain management can help companies reduce lead times when businesses receive raw materials and more, improve product quality, and ensure timely delivery, enhancing overall customer satisfaction.
Differences Between Value Chain vs Supply Chain
Explanation of the Key Differences Between the Two Terms
The key differences between supply and value chains are in their focus, scope, and activities.
Focus
The value chains focus on the internal activities of a company, including the activities done to create a product or service and delivering it to customers. The supply chains, on the other hand, aim to transform inputs and the external activities involved in acquiring the raw materials, components, or services needed to create finished goods, as well as the transportation and distribution with channel partners to deliver the final product to the end-user.
Scope
The value chain is limited to the activities within a company, while the supply chain focuses on the entire network of organizations involved in the creation and delivery of a finished goods or services.
Activities
The value chain involves primary activities such as inbound logistics, operations, outbound logistics, marketing and sales, and service, as well as support activities such as technology development, human resources management, procurement, and firm infrastructure. The supply chain involves planning, sourcing, making, delivering, and returning.
Examples of How Companies Can Achieve Better Performance by Integrating Value Chain and Supply Chain
While supply and value chains serve different purposes and involve different activities, the two chains are interdependent and can be integrated to achieve better performance. By integrating the value chain and supply chain, companies can enhance their operational efficiency, lower costs, and improve customer satisfaction.
For example, by using technology to track inventory levels and demand patterns, companies can optimize their inbound logistics, reducing the amount of inventory held while ensuring a reliable supply of high-quality raw materials. Additionally, by integrating their production processes with their supplier’s processes, companies can reduce lead times and improve product quality and meet every customer request.
Why Choose SFL Worldwide?
SFL Worldwide is a global logistics company that provides end-to-end solutions to simplify processes for businesses. With over 15 years of experience in the industry, SFL Worldwide has the expertise and resources to manage all aspects of business management from procurement to delivery, and has a positive impact on a business’s value chain. By choosing SFL Worldwide, businesses can benefit from improved efficiency, reduced costs, and overall customer satisfaction.
CHOOSE SFL WORLDWIDE, SAY GOODBYE TO OBSTACLES.
Your partner in delivering packages of varying attributes. Our customer testimonials page speaks volumes about the quality of work we provide. We are always happy to serve you here at SFL Worldwide.
Gain Competitive Advantage with SFL Worldwide's Supply Chain Services
SFL Worldwide offers a range of services, including procurement, transportation, warehousing, and distribution. These services are designed to simplify the process for businesses of all sizes, allowing them to focus on their core operations while leaving the logistics to the experts. SFL Worldwide’s services are backed by advanced technology and a team of experienced professionals who are committed to delivering high-quality solutions to their clients.
Conclusion
The value chain and supply chain frameworks are essential for companies seeking to sustain superior performance and gain a competitive advantage. While the value chain focuses on the internal activities of a company, the supply chain encompasses the entire network of organizations involved in the creation and delivery of a product or service. By effectively managing both frameworks and integrating them where possible, companies can optimize their operations, lower costs, and enhance customer value. Ultimately, by delivering high-quality products and services that meet or exceed every customer request, companies can achieve sustainable success and maintain their competitive edge in the market.
FAQs About Supply Chain Management
Supply chain plays a vital role in operations of a business as it is responsible for managing the entire process of delivering goods and services to customers. It involves coordinating activities such as order processing, procurement, transportation, warehousing, and distribution in fulfillment centers to ensure that products are delivered to customers in a timely and cost-effective manner. Effective management of this process can help companies lower costs, improve customer satisfaction, and gain a competitive advantage.
The key steps involved in the supply chain process include procurement, transportation, warehousing, and distribution in fulfillment centers. Procurement involves identifying and selecting suppliers and negotiating contracts. Transportation involves moving goods from one location to another, while warehousing involves storing and managing inventory. Distribution involves delivering products to customers.
Companies can optimize their processes by using technology, data analytics, and efficient processes. For example, using RFID technology to track products can help companies manage their inventory levels, while data analytics can help them identify trends and patterns in demand. By streamlining processes and improving communication between suppliers and customers, companies can minimize costs and maximize profits.
Efficient supply chain can provide numerous benefits to a company, including cost savings, improved customer satisfaction, increased productivity, and reduced lead times. By streamlining processes and improving communication between suppliers and customers, companies can minimize costs and maximize profits.
Some common challenges faced by companies in managing their supply chains include inventory management, transportation, and communication issues. Managing inventory levels can be challenging, especially when dealing with perishable goods or items with short shelf lives. Transportation issues such as delays or disruptions can also impact the supply chain process. Communication issues between suppliers and customers can lead to misunderstandings and delays. This requires companies to address these challenges proactively and continuously improve their processes to gain a competitive advantage.
Feel free to get in touch with one of our expert advisors to get answers to supply chain faqs and learn how to optimize your supply chain vs value chain.
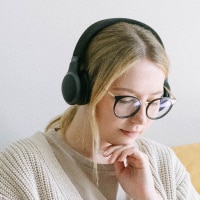
I’m Tammy Waller, a supply chain and logistics specialist with over 10 years of expertise. I’ve been an author and SFL employee for over 10 years.
As an author, I’ve been able to teach others. I love guiding users through supply chain and logistics operations.
I have substantial experience managing logistics operations, supply chain management, transportation, inventory management, and warehousing in shipping-moving and logistic services. I’ve worked on many worldwide logistics and supply chain projects, honing my abilities in negotiating rates, scheduling shipments, and managing vendors.